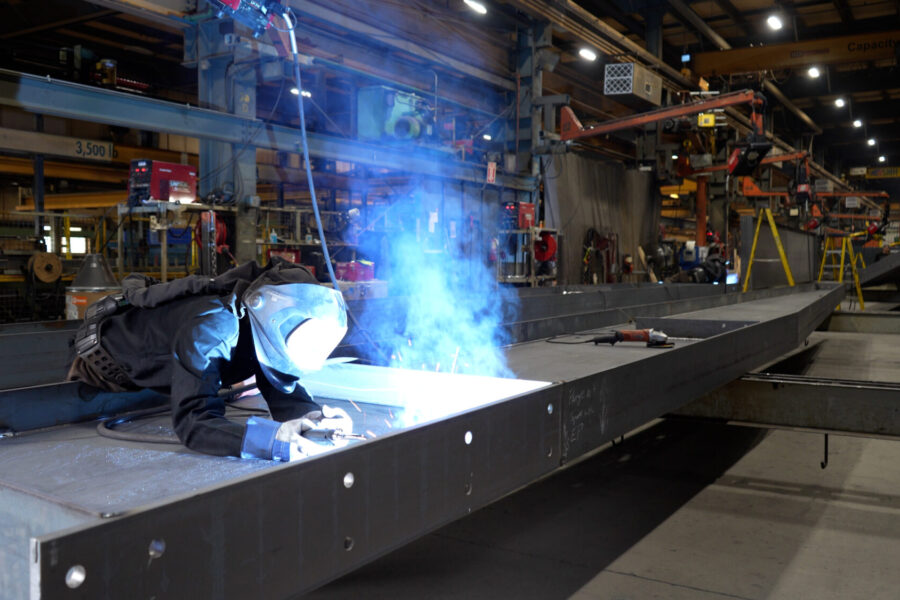
The Challenge: Labor Shortages and Scalability
Rural Location, Skilled Labor Gaps, and Growing Demand
Located in Elmer, Ontario, Steelway has long faced challenges familiar to many fabricators—chief among them: labor shortages, especially when it comes to experienced welders.
“Finding skilled welding labor is very challenging, especially being out here in a rural area,” shares Jake Giesbrecht, Director of Product Excellence at Steelway. With expanding production volumes and rising complexity in structural designs, the company needed a reliable solution to scale efficiently without sacrificing quality.
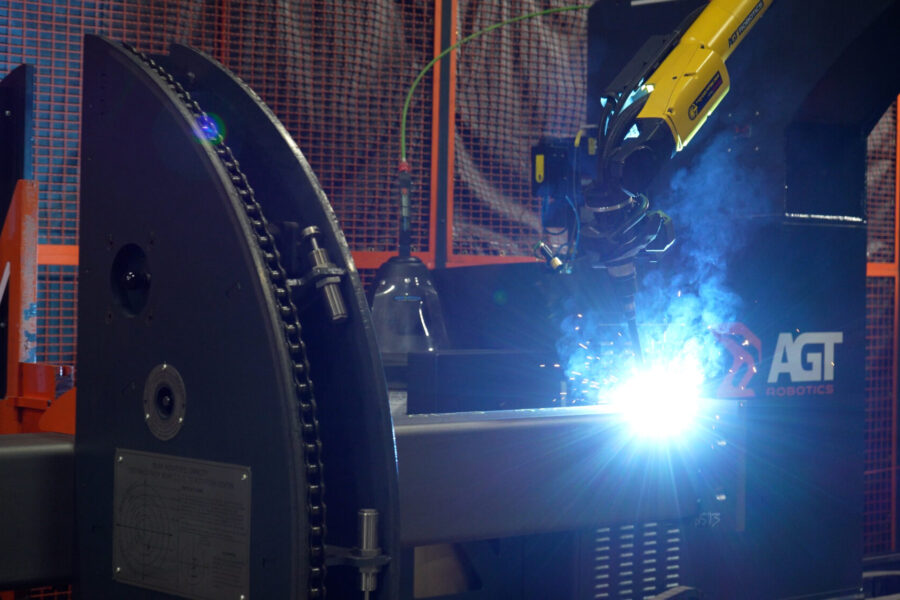
The Solution: BeamMaster Robotic Welding System
Welding All Four Sides—Faster, Easier, Smarter
After discovering AGT Robotics at Fabtech in Chicago, the Steelway team was impressed by the BeamMaster’s unique ability to rotate and weld beams on all sides. Unlike their previous single-sided robotic solution, the BeamMaster enabled full 4-side welding of three-plate beams—significantly reducing manual work and production time.
“This system is better, easier to learn, and capable of more welding,” says Randy Thiessen, Robotic Weld Cell Coordinator. “It rotates the beam and welds all four sides. For the amount of welding this system does, it is faster than what we had before.”
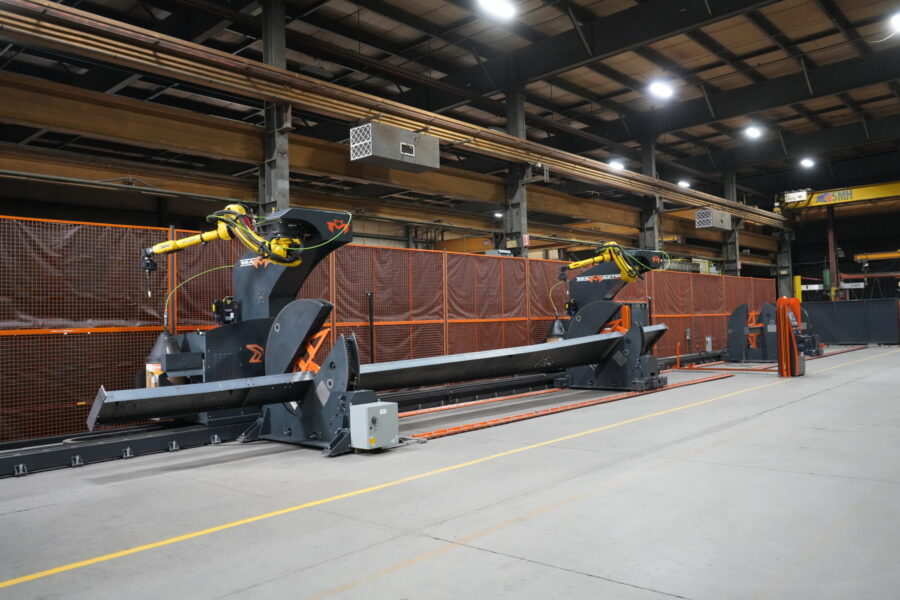
Scalable, Flexible Integration
From One Robot to Two—and More on the Horizon
Impressed by the BeamMaster’s performance, Steelway quickly expanded their system by adding a second robot and extending the welding zone by over 14 feet. This allowed them to handle longer beams (up to 60 ft) and work across dual zones—one for larger components, another for smaller parts—maximizing uptime and throughput.
“We added a second robot and extended the zone to optimize for longer pieces,” Giesbrecht explains. “It made us more productive, and now our welders can focus on critical repairs rather than repetitive welds.”
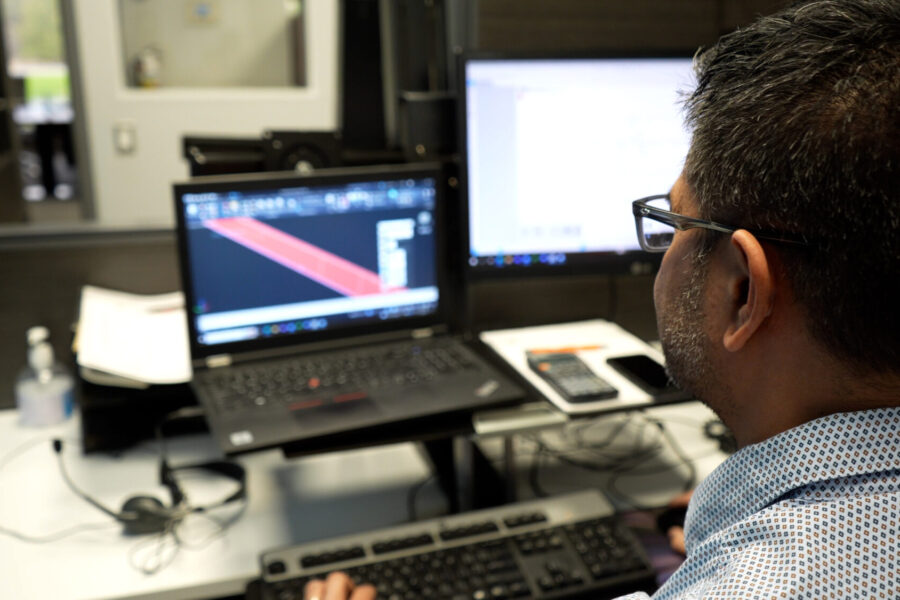
Smarter Programming with Cortex & Advance Steel
A Fully Digital Workflow from Design to Weld
Steelway’s process begins with modeling their buildings in Advance Steel. From there, IFC files are exported directly into AGT’s Cortex software, enabling automatic robot programming—no manual input required.
“We export IFC files into Cortex, and it builds the programs automatically. We’re very proud of how it’s producing,” says Giesbrecht. “It’s a game-changer for us.”
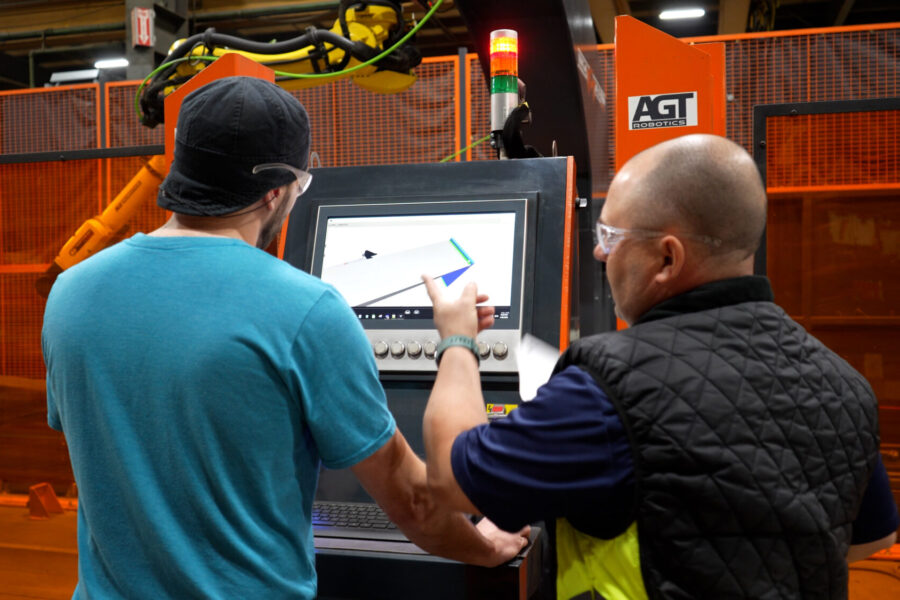
The Result: Increased Efficiency, Productivity, and Future Growth
Robots and Welders Working Hand-in-Hand
The BeamMaster hasn’t replaced Steelway’s workforce—it’s empowered it. Manual welders now focus on high-value tasks while the robot handles long, repetitive welds. This intelligent division of labor has improved weld quality, increased output, and helped the company meet tight deadlines with ease.
“The future is more robots. We’re looking at adding even more to our hot-rolled section,” Giesbrecht shares. “The BeamMaster has been a great investment, and we’re excited to continue building on this success.”
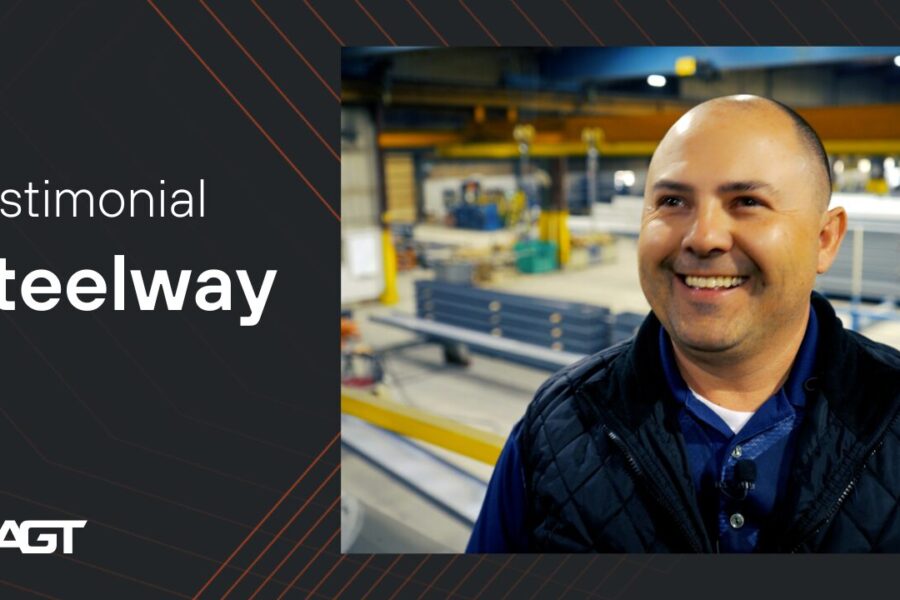
See It in Action
Watch the Full Testimonial
Want to see how Steelway Building Systems modernized their welding workflow with AGT Robotics? Watch their full story and discover how robotic automation can elevate your shop’s performance.
Is Robotic Welding Right for You?
If you’re facing labor shortages or looking to increase welding productivity, AGT Robotics can help. Contact us today to learn how automation can transform your operations—just like it did for Steelway.
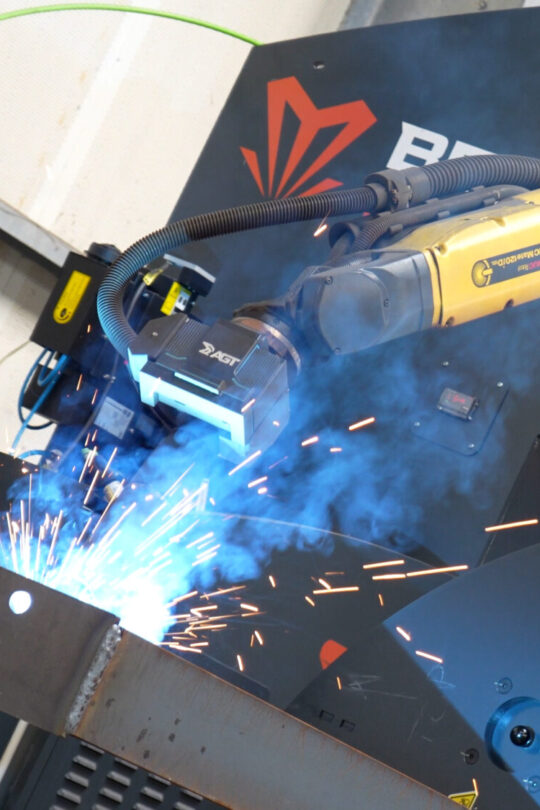
Latest AGT News
Stay informed with our in-depth articles on the latest innovations and developments in the world of robotics and automation.